Did you know that over 70% of all playground accidents happen from children falling?
That’s why a proper fall zone playground design isn’t just a safety requirement; it’s necessary to protect our children. Grass might seem like an affordable option, but experts don’t recommend it as a fall zone material. Specific materials like Engineered Wood Fiber (EWF) and poured-in-place rubber surfacing give proven protection for playground fall zones.
Creating safe playground fall zones can feel overwhelming. You need to calculate the correct dimensions (six feet in all directions from all equipment) and pick appropriate surfacing materials. The proper knowledge and implementation can substantially reduce the risk of serious injuries.
Let’s take a closer look at everything you need to know in playground fall zone standards to keep children safe during play.
Understanding Playground Fall Zone Fundamentals
Fall zones are vital safety elements in playground design. These special areas act as protective spaces around playground equipment and protect children when they fall during play.
What are these zones, why do they matter, and who sets the rules for them?
What defines a fall zone in playground design
A fall zone (some people call it a use zone) is:
“The surface under and around a piece of equipment onto which a child falling from or exiting from the equipment would be expected to land.
Safety guidelines require these protective areas to extend at least six feet in all directions from the edges of stationary playground equipment.
Each type of equipment needs specific fall zone measurements:
- Slides: Slides measuring four feet or less need fall zones that extend six feet from the end. Taller slides need zones that stretch the entrance height, plus four feet from the exit.
- Swings: These need larger fall zones. The space should extend twice the height of the pivot or swing hanger in front and behind the seats, plus six feet on each side of the support structure.
- Climbing equipment: Fall zones must stretch six feet beyond the equipment in all directions.
The concept of “critical fall height”:
Critical fall height represents the maximum distance a child can fall without risking a life-threatening head injury. This measurement helps determine how deep and thick your protective surface needs to be.
Why fall zones are significant for child safety
Statistics prove that fall zones matter. More than 70% of playground accidents happen when children fall.
Well-designed fall zones help to:
- Lower injury severity rather than stop falls completely
- Cut down the risk of life-threatening injuries, especially head injuries.
- Absorb shock when falls happen.
- Set clear boundaries for safe equipment use.
The material used in fall zones plays a big part in preventing injuries. Concrete, blacktop, packed earth, or grass don’t work under play equipment. These surfaces can’t absorb enough shock from falls.
Research shows that proper safety surfacing can reduce the risk of severe head injury by 75% and bone fractures by 79%. Fall zones aren’t just a design choice; they’re essential for safety.
Several expert organisations create and update fall zone standards:
U.S. Consumer Product Safety Commission (CPSC) writes complete guidelines for public playground safety. Their Handbook for Public Playground Safety looks at fall risks and equipment impact. They strongly advise against installing playgrounds on concrete, asphalt, or paved surfaces.
American Society for Testing and Materials (ASTM) developed the ASTM F1487 voluntary safety standards for playground equipment. These standards give detailed specs for safety performance and testing methods, especially for equipment made for children ages 2–12.
British and European Standards (BS EN 1176 and BS EN 1177) focus on good practices in playground equipment design, manufacturing, and maintenance. BS EN 1177 specifically covers surfacing standards and critical fall height requirements.
Health and Safety Executive (HSE) suggests appropriate fall zone designs and supports protective surfacing as a safety measure.
These organisations continually improve their standards based on injury data, testing, and new playground designs. They aim to create safer play spaces while maintaining the beneficial risks that help children develop.
Essential Fall Zone Dimensions and Measurements
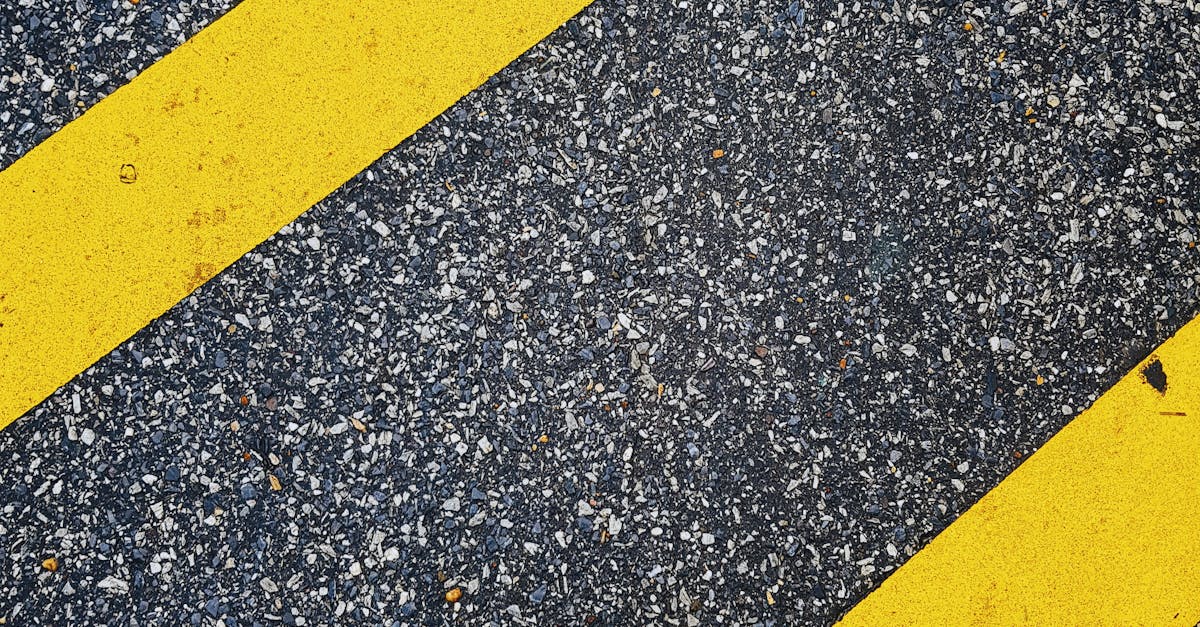
Good measurements make all the difference between proper and poor fall zone protection. Safety organisations set these dimensions after an extensive longitudinal testing and injury data study.
General equipment fall zone requirements
- Playground fall zones need a minimum of six feet of clearance from the edge of stationary play equipment in every direction.
- Equipment with fall heights between 0.6m and 1.5m needs a fall zone that extends at least 1.5m around it.
- The required distance grows linearly as fall heights increase between 1.5m and 3m.
- It reaches 2.5m for equipment with a maximum fall height of 3 m.
- Fall zones can’t overlap for equipment taller than 24 inches above ground. This means play structures must be at least twelve feet apart.
- Equipment under 600mm high doesn’t need a protective surface, but some cushioning helps reduce impact.
- The critical fall height should stay under 3 meters. This is the maximum height where life-threatening head injuries are unlikely.
- No playground equipment should be taller than this limit.
Specific requirements for slides and elevated platforms
Slides need extra attention because kids use them differently. For slides up to 4 feet high, the fall zone at the exit must extend 6 feet from the end. Taller slides need more space; add 4 feet to the entrance height to calculate the required distance.
Each slide type has its own rules:
- Type 1 slides (short run-out section): need 2000mm impact area past the end
- Type 2 slides (long run-out section): need 1000mm impact area past the end
The fall height of elevated platforms is measured from platform to ground. This measurement determines the size of the fall zone and the depth of the safety surface.
Swing set fall zone calculations.
Swings need the most significant fall zones of any playground equipment. The front and back areas must be twice the pivot or swing hanger’s height. The sides must extend at least 6 feet from the support structure.
The math works like this: protected area length (L) should go 1.75 meters past the swing’s movement limits. Calculate each side as L = (A x 0.867) + 1.75 meters, where A is the swing suspension length.
Single-point swings, often called tyre swings, need a circular protected area from their rest position. The radius follows the same formula: R = (A x 0.867) + 1.75 meters. This allows for a 60° swing angle anywhere.
Special considerations for climbing equipment
Climbing structures are tricky because kids might fall from many spots. Their fall zones must extend 6 feet in all directions from the structure’s edges.
Play equipment needs a clear, safe 2-meter zone around it. Nothing that could hurt during a fall should be in this space.
Kids should keep three points of contact while climbing. However, fall zones must plan for falls from the highest reachable point, not just from the handholds or footholds.
When calculating fall zones, the highest point kids might reach matters more than just the intended handholds. Even with rails, supports, or seats, calculations must account for adventurous children who might climb higher.
Critical Fall Zone Surfacing Materials
Impact attenuation requirements
Impact attenuation shows how well a surface absorbs shock and lowers the risk of serious injury.
ASTM F1292 requires all playground surfacing materials to meet two key performance criteria:
- g-max score not exceeding 200
- A Head Injury Criterion (HIC) score not exceeding 1000.
These scores measure the shock from an impact and show how acceleration relates to head trauma risk.
Tests must assess samples at three reference temperatures: 25°F, 72°F, and 120°F. This ensures materials work well in all seasons. The critical fall height from these tests shows the highest point at which a fall would likely not cause life-threatening head injuries.
Loose-fill material options and maintenance
Loose-fill materials work by trapping air between particles to absorb impact. Here are the options:
- Engineered Wood Fiber (EWF): Meets ASTM F2075 standard and protects falls up to 10 feet with a 9-inch depth
- Bark/Wood Chips: Guards against falls up to 7-10 feet at proper depth. It needs regular topping up.
- Sand: Protects falls up to 4 feet with a 9-inch depth
- Pea Gravel: Guards against falls up to 5 feet with a 9-inch depth
- Rubber Mulch: Great shock absorption and lasts longer, though costs more upfront
Regular maintenance is vital since these materials compact and scatter. Areas under swings and slide exits need weekly raking and periodic refills.
Unitary surfacing solutions
Unitary surfaces like poured-in-place rubber, rubber tiles, and synthetic turf create smooth, available surfaces that need less upkeep than loose-fill options. Poured-in-place rubber guards against falls from up to 10 feet with just 4.5 inches of thickness.
Manufacturers must test these surfaces to meet ASTM F1292 standards and provide fall height certification. The higher initial cost pays off since these surfaces only need occasional cleaning and repairs.
Comparing cost vs. safety benefits
Original costs can vary greatly. Loose fill materials cost less upfront, but ongoing maintenance costs add up because loose materials need yearly refills.
Unitary surfaces help children with mobility challenges move around better despite higher upfront costs. The final choice comes down to balancing maintenance needs with budget while meeting safety standards.
Fall Zone Compliance and Inspection Protocols
To maintain compliance, playground fall zone standards need complete documentation and regular inspections. A well-documented fall zone keeps children safe and meets legal and insurance requirements.
Documentation requirements for fall zones
Every playground fall zone installation needs complete documentation to prove safety compliance. We must maintain:
- Standard compliance verification: Written confirmation that equipment and surfaces comply with relevant standards like EN 1176 and EN 1177
- Manufacturer certification: Documentation from suppliers confirming that protective surfacing is tested in accordance with BS 7188 and EN 1177
- Installation confirmation: Written assurance that equipment is installed according to manufacturer instructions
- Test certificates: Certificates from recognised test houses (BSI, CST, RAPRA) that verify surfacing materials meet impact attenuation requirements
- Post-installation inspection report: Documentation of the original safety assessment after installation
Playground managers should keep hosted records of all inspections, repairs, and maintenance activities to prove ongoing compliance and create accountability.
Regular inspection checklist
Playground managers must set up a well-laid-out inspection protocol after installation. The British and European safety standard BS EN1176 and the Health and Safety Executive strongly recommend that independent qualified bodies inspect all play areas at least once yearly.
A complete inspection schedule has:
Routine inspections (weekly minimum): Look for vandalism, debris, apparent defects, and simple equipment condition. Check fall areas for proper surface material depth and rake to fill low areas.
Operational inspections (monthly/quarterly): Get into wear and tear, loose fastenings, and surface integrity.
Annual complete inspections: Independent specialists must conduct these to verify long-term safety compliance. These inspections check structural integrity and standard compliance and create detailed written reports with risk ratings for each item.
Whatever the inspection frequency, playground managers should verify that protective surfacing extends at least 6 feet in all directions from play equipment. The surface must be sufficiently deep (at least 12 inches of wood chips, mulch, sand, or pea gravel).
Any inspection program is worthless without a system to fix identified issues quickly.
Common Fall Zone Violations and Their Solutions
Inadequate surfacing depth
Use and weather cause loose-fill materials to compress by at least 25%, which creates dangerous conditions without proper upkeep. Playground sand needs a minimum depth of 12 inches. Most violations happen because the depth isn’t enough.
The best fix involves setting up regular material top-offs, which is vital in areas where kids play most, like slide exits and under swings. In these spots, the most material gets pushed away. Wear mats in these busy zones can reduce material displacement significantly.
Improper fall zone dimensions
Safety standards don’t work when playgrounds lack enough clearance around equipment. Protected areas should stretch at least 1.5 meters around equipment with fall heights between 0.6 and 1.5 meters. Taller equipment (1.5-3m) needs even more space around it.
Your playground layout might need changes to achieve the correct spacing. Equipment pieces with overlapping fall zones must be relocated or removed to maintain the required six-foot gap between structures.
Surfacing material migration issues
Kids playing and weather conditions push loose materials away from where they should stay, creating zones without enough protection.
Here’s what helps:
- Put containment curbs around fall zones
- Add geotextile fabric under loose fill so that it won’t mix with the soil
- Rake and spread materials back where needed, especially in busy spots
Addressing drainage problems
Inadequate drainage allows water to pool in playground areas and creates multiple risks. Water makes surfaces slippery, breaks down surfacing faster, helps bacteria grow, and can shut down the entire play area.
French drains – trenches filled with gravel and perforated pipes work well as a solution. You could also add sump pits outside fall zones or use trench systems at the playground’s lowest points. Thoughtful playground planning should include a drainage design that suits local weather patterns.
Conclusion
Playground fall zones protect children from serious injuries during play. Safety requirements, proper materials, and regular maintenance can substantially reduce playground accidents.
Several interconnected factors determine fall zone safety. Quality surfacing materials must match appropriate dimensions. Regular inspections ensure ongoing protection. Quick responses to common violations help maintain the highest safety standards.
Your playground’s fall zones need verification and upgrades to prevent serious injuries. Check the surfacing depths and measure fall zone dimensions. Schedule professional inspections regularly. These basic steps create safer spaces where children play, learn, and grow confidently.
FAQs
Q1. What are the essential fall zone requirements for playgrounds? Fall zones should extend at least 6 feet in all directions from play equipment. The surfacing material should be at least 12 inches deep for loose materials like wood chips or sand. For equipment over 4 feet tall, additional fall zone space may be required. Regular inspections and maintenance are crucial to ensure these requirements are consistently met.
Q2. How do fall zones differ for various types of playground equipment? Different equipment types have specific fall zone requirements. For slides, the fall zone should extend 6 feet from the slide end for those 4 feet or less in height, while taller slides need more space. Swings require larger fall zones, extending twice the height of the pivot point in front and behind. Climbing equipment needs a 6-foot fall zone in all directions from its perimeter.
Q3. What are the best surfacing materials for playground fall zones? The most effective surfacing materials include engineered wood fibre, poured-in-place rubber, rubber mulch, and rubber tiles. These materials offer excellent shock absorption and meet safety standards. While loose-fill materials like sand and pea gravel are options, they require more frequent maintenance. The choice often depends on factors such as budget, maintenance capabilities, and accessibility needs.
Q4. How often should playground fall zones be inspected? Playground fall zones should undergo routine inspections at least weekly to check for obvious hazards or defects. More thorough operational inspections should be conducted monthly or quarterly to examine wear and tear. Additionally, an annual comprehensive inspection by an independent specialist is crucial to verify long-term safety compliance and structural integrity.
Q5. What are common fall zone violations, and how can they be addressed? Common violations include inadequate surfacing depth, improper fall zone dimensions, and material migration. To address these issues, regularly top off loose-fill materials, ensure proper spacing between equipment, install containment curbs, and implement effective drainage systems. Prompt attention to these issues helps maintain safety standards and prevent serious injuries.
Get In Touch
Whatever the size or scope of your landscaping project, we are confident that we can accommodate your needs and provide an end product that matches or even exceeds your initial expectations.
We can provide free, competitive, and comprehensive, detailed quotes based on your plans upon request.
We’ll provide a detailed, free quotation that matches your needs with no strings attached. To contact us, click the button below and fill out our form.